Slurry Hose Built Tough For Maximum Wear Life
Getting a slurry hose that is built to withstand abrasive applications versus a poorly generic hose can mean the difference when it comes to meeting your dredging project deadline or running into problems. When looking for a slurry hose, you want to look for flexibility, rubber thickness and build construction.
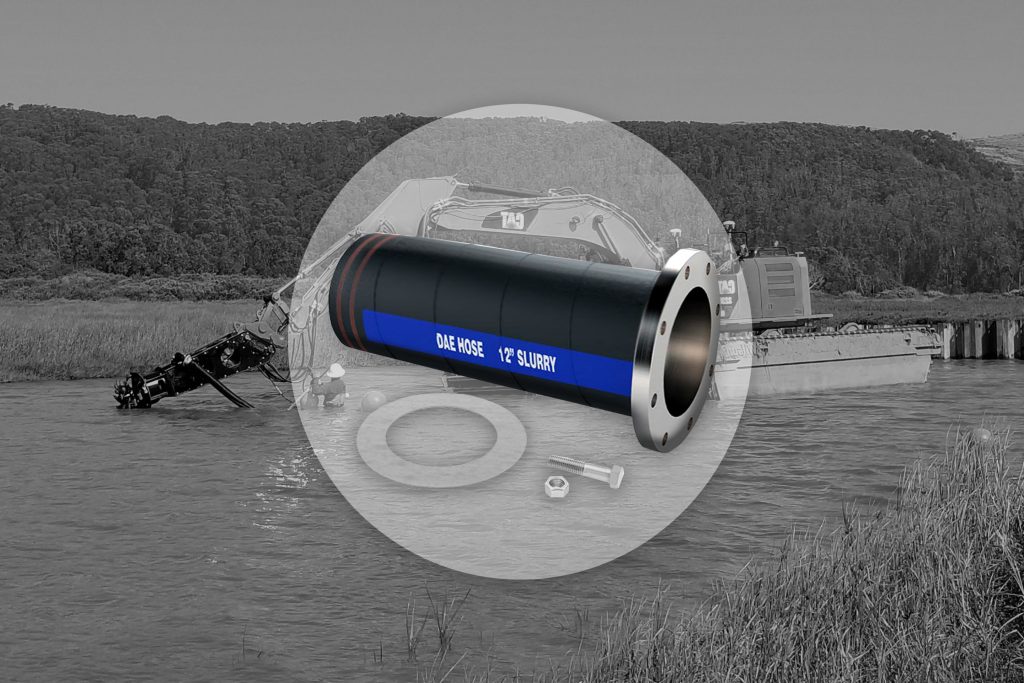
Why Use a Slurry Hose?
Compared to rigid and heavy steel pipelines, slurry hoses have a distinct advantage over pipelines due to their flexibility. Slurry hoses are able to be maneuvered on-site when the situation calls, unlike a set in place metal pipeline.
Applications that require the pump to be moved around and relocated like dredging, benefit greatly from utilizing a slurry hose.
Using traditional steel pipes, welding would be required to modify location. Being able to easily fit into existing pipe structures, allows for modifications to be made on the fly without the hassle of having to shut down the operation to make adjustments.
What To Look For In a Slurry Hose
There are several variables that come into play when choosing a slurry hose for your project. We use an easy to use acronym STAMPED to help make the process easy to narrow down which slurry hose you need for the job:
S- Size (Measure the sizing of outside diameter, inside diameter and total length including tolerances and fittings)
T- Temperature (Temperature of the material including ambient weather temperature)
A – Application (Orientation of the hose, configuration, routing)
M – Material (Concentration of solids, PH level, flow rate, velocity, type of material)
P – Pressure (Maximum pressure within a system. Take note of the hose and hose end ratings to not be less than the maximum operating pressure system.)
E – Ends (orientation, attachment methods, coupled or uncoupled, hose style)
D – Delivery (How fast does the job need to be done)
By using the acronym above you can find select the right hose for your application. If you do not want to go through the hassle of having to do the research alone, contact one of our experts at (760) 821-8112 or info@daehose.com
Installing a Slurry Hose To Pipeline
The majority of the time, slurry hoses and pipelines are defined by their inner diameter. During highly abrasive applications such as mining, slurry hoses have an internal lining to withstand and minimize wear/tear on the hose. Rubber linings are also utilized within the main metal pipelines during highly abrasive pumping operations.
Rubber linings play an important role but they can reduce the inner diameter and make it more narrow inside. When pairing a hose to an existing pipeline, keep a note of the outer diameter, thickness, and if there is a lining or not.
By doing these checks, the inner diameter of the slurry hose and pipeline will have an optimal flow throughout the system.
Slurry Hose Fittings and Connectors
There are several different fittings and ends that can be attached to the end of a slurry hose to attach it to another section of the hose, extend the length, attach to the pump itself and other applications.
Couplings — have the ability to connect two segments of pipe or hose into one single piece. They allow for easily swapping out sections of pipe or hose. They do not come in direct contact with the material, so they are not subject to harsh abrasion or wear. This allows them to be easily reused when replacing slurry hoses.
Gaskets – acts as a seal for couplings. Gaskets reduce turbulence and help regulate the flow caused by uneven diameters.
Flanges and couplings are classed based on the material they are comprised of, usually iron or steel. Each class is different, classified on several different aspects such as dimensions, operating pressure, and temperature. Most slurry hoses use ANSI (American National Standards Institute) class flanges, which are standardized across the industry.